The introduction of new procedures or the implementation of change, no matter how insignificant it may seem, has the ability to impact on the quality of the service being provided or indeed on the quality of the product being handled. However changes are always necessary and procedures must be improved, new equipment and processes must be introduced; it’s how these changes are controlled that negates the possibility of any negative impact on the customers’ product or indeed on the quality of service we provide to the customer.
At Store-All Logistics we have a Standard Operating Procedure (SOP) specific to how change is controlled that all staff at all levels are trained on. Some key aspects of this are:
- Proposal of a change
- Classification of a change
- Approval of a change
- Implementation of a change
All changes must be approved by our own Quality Department, however there are also classifications of changes that we would run by our customers Quality Department for approval before the change could be introduced. This ensures that our customer is always in control of their products and how they are stored, handled and distributed.
The key strengths of our Quality System include:
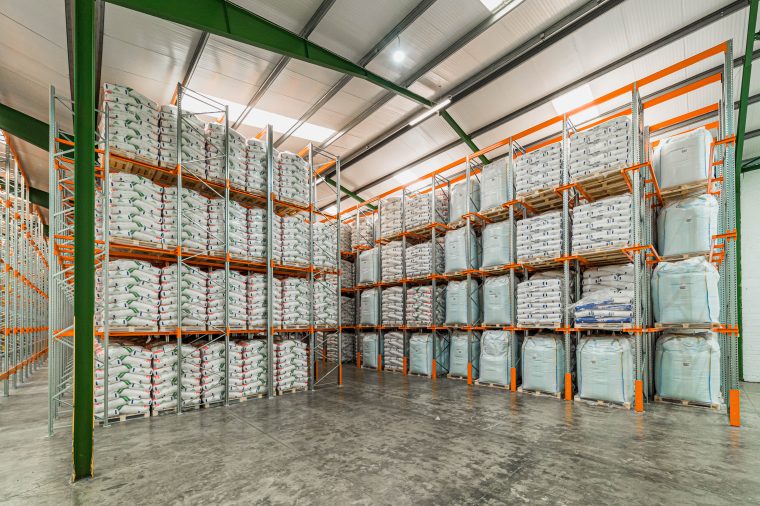